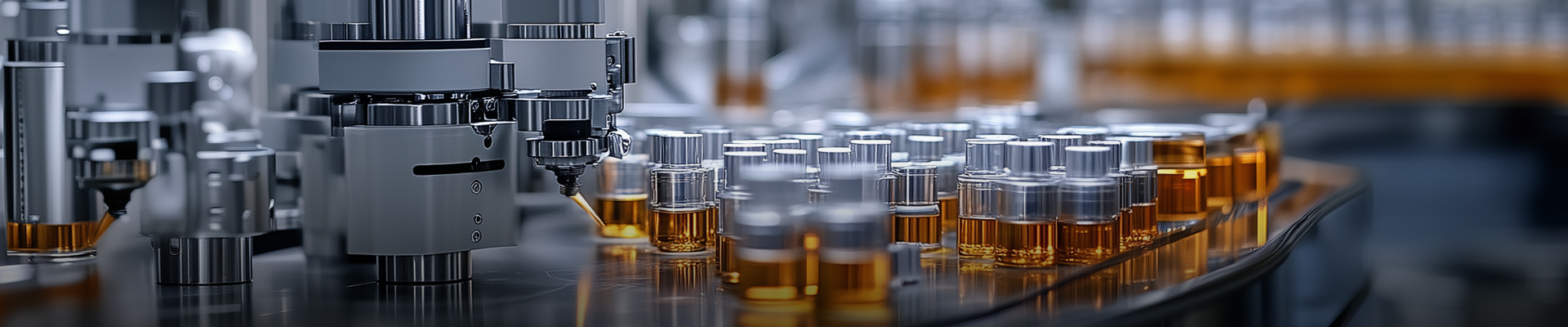
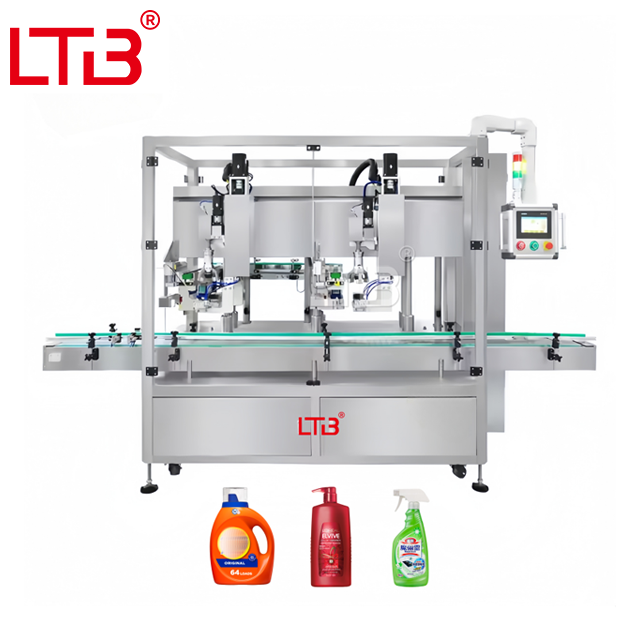
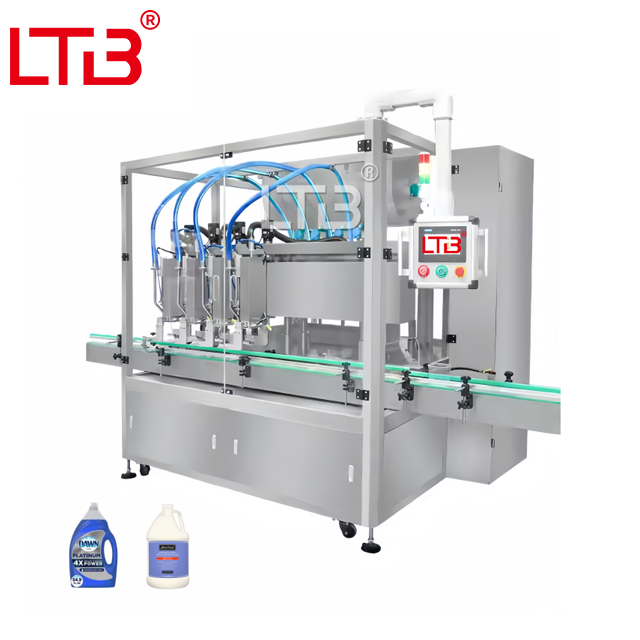
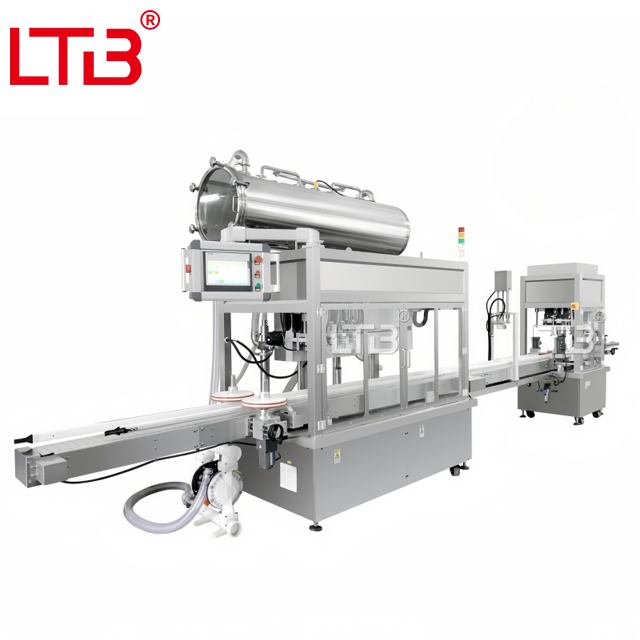
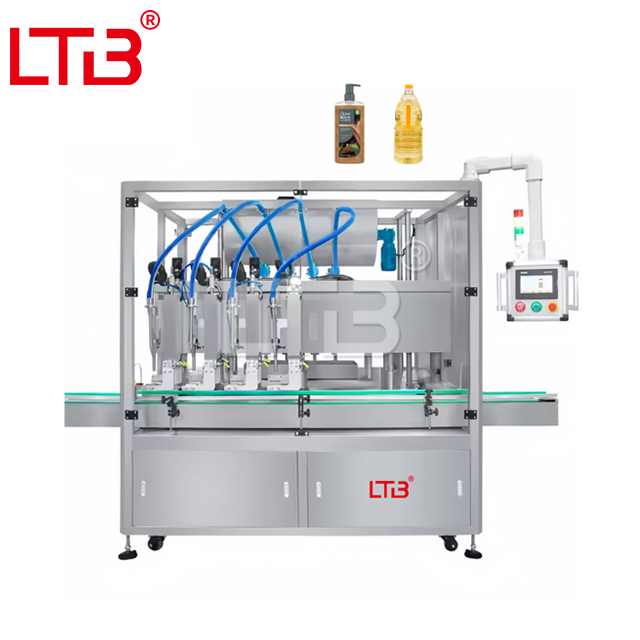
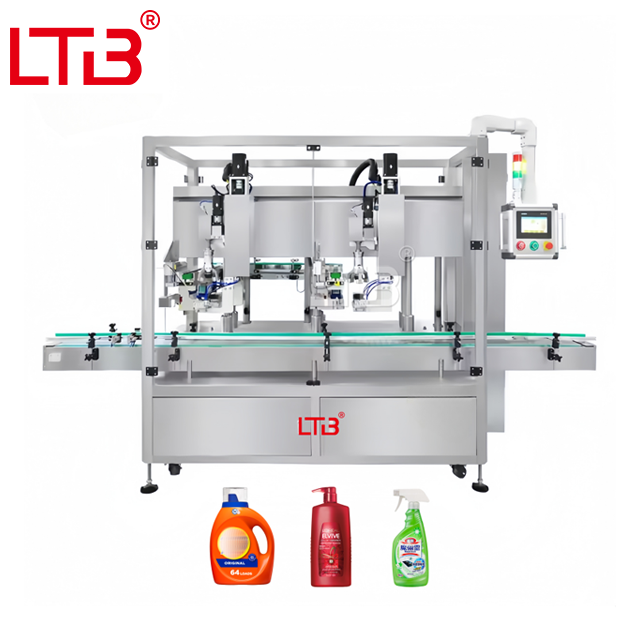
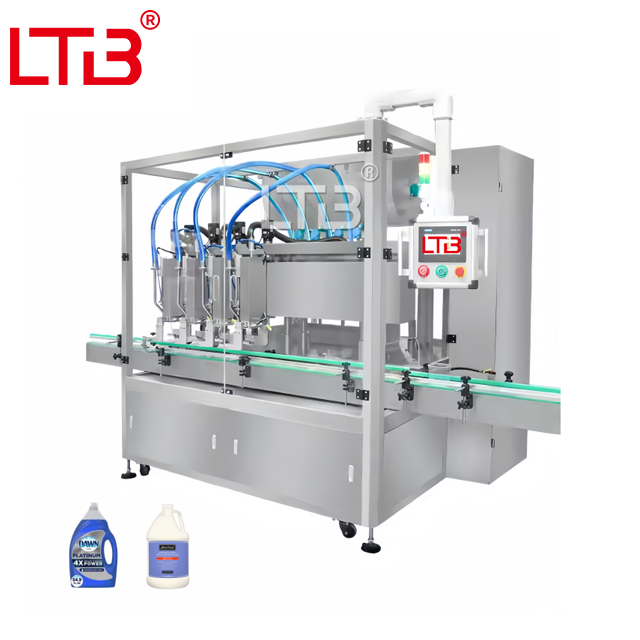
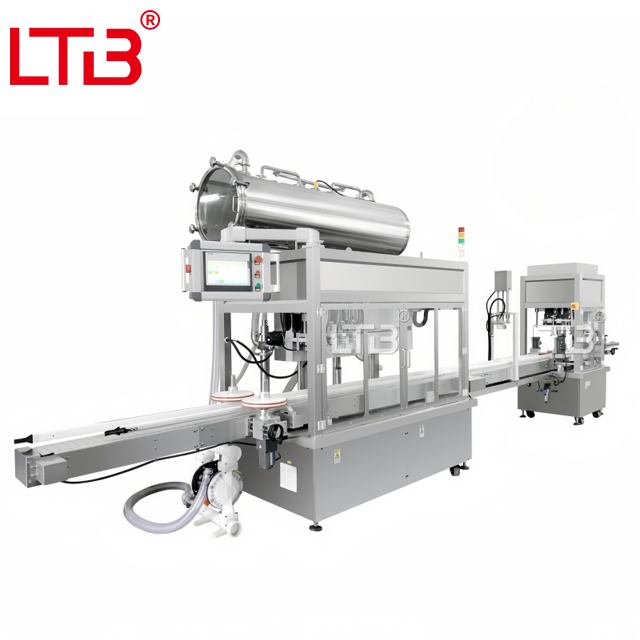
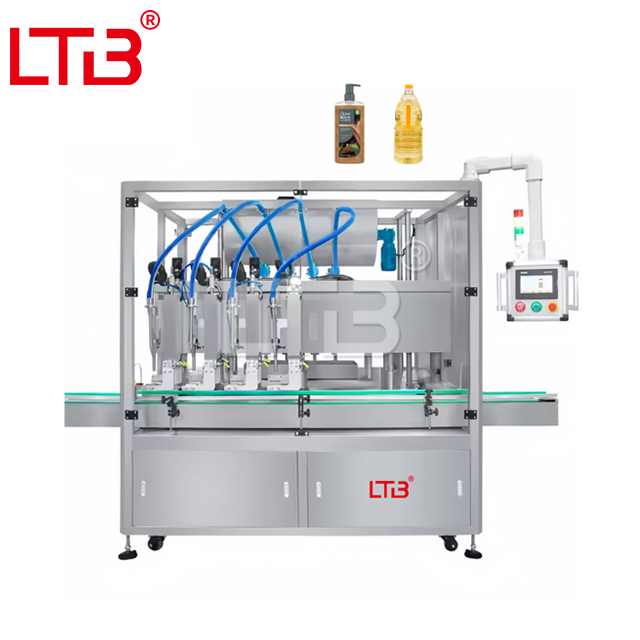
The Automatic tracking filling machine is the first choice for big capacity bottle, especially like daily chemical, cosmetics, skincare, and liquid food sauce industries. It handles diverse liquid and paste products, from liquid hand soaps, shampoo, detergent to high - end serums and various sauces. The machine adapts to different container sizes and shapes, ensuring accurate dosing for each product.
Equipped with an advanced tracking system, its filling nozzles precisely follow container movement. It offers high - precision filling with adjustable volumes, maintaining accuracy even at high speeds. This versatile machine can handle different product consistencies and container materials, providing a reliable, efficient, and accurate filling solution for modern packaging needs.
PRODUCTS DESCRIPTION
Description
Advantages
Technical Parameters
Filling Nozzle | 2 Nozzles | 4 Nozzles | |
Filling Type | Tracking type, the filling nozzle moves along with the bottle during the filling process | ||
Filling Volume | 5-150ml / 10-250ml / 30-500ml / 50-1000ml / 250-2500ml / 300-3000ml / 500-5000ml | ||
Filling Speed (Water test. Actual output is related to material volume and viscosity) | 40-50bottles/min | 50-80bottles/min | |
Material | All product contact part are made of stainless steel 316L/304 | ||
Filling Accuracy | ±1% | ||
Main Parts | Siemens PLC, Panasonic Servo Motor, Schneider Electronic, Festo/AirTAC pneumatic component, etc. | ||
Remark | The filling volume and speed are customized according to client's product and requirement, contact us to send your requirement :) |
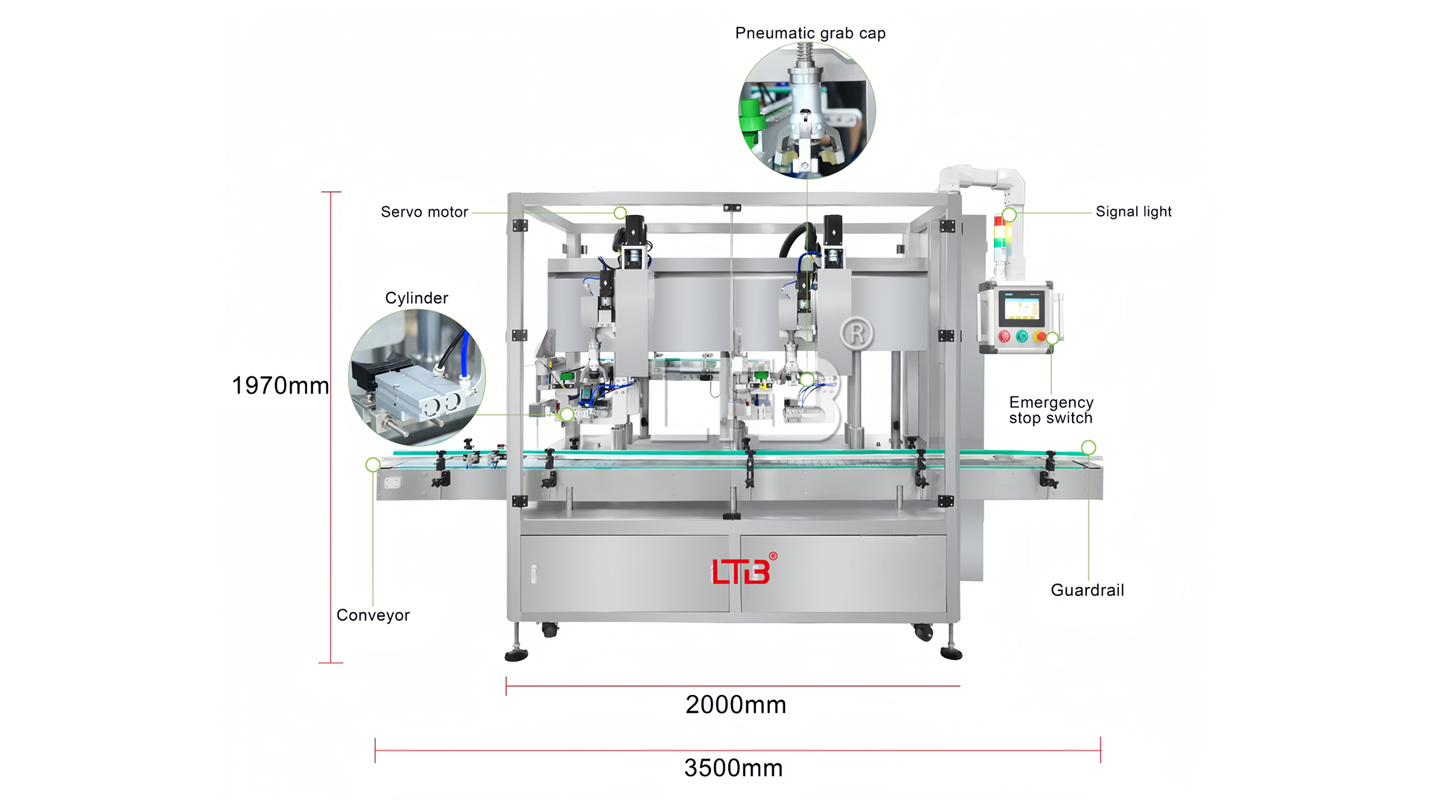
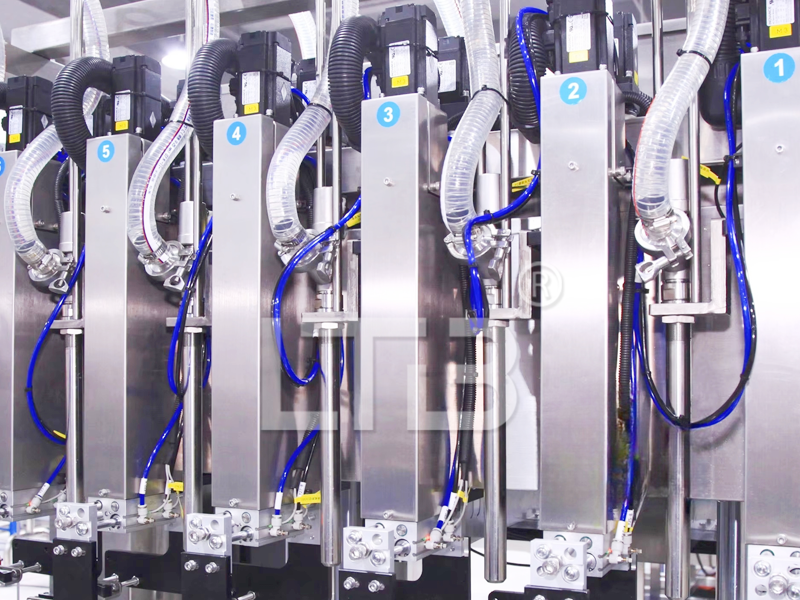
Tracking Filling Head
1. Advanced Tracking Filling Mechanism:Our filling machine is equipped with tracking filling heads that synchronize with the movement of bottles. This innovative approach significantly enhances production efficiency in contrast to traditional methods where bottles need to be halted for filling. By enabling continuous bottle movement during the filling process, it minimizes production downtime and maximizes throughput.
2. Customizable Configuration:The number of filling heads can be tailored to meet specific customer production requirements. Whether for small - scale or large - scale production, this flexibility ensures optimal productivity. Additionally, the filling process offers remarkable accuracy, with an error margin of only 0.5%.
3. User - friendly Operation:Each filling head is equipped with touch - screen controls. This intuitive interface allows operators to easily adjust and monitor filling parameters, ensuring seamless operation and consistent filling quality.
Material Pipe
1. Premium Material Selection:Our filling machines feature two types of material pipes. For applications involving food - contact materials, we utilize high - grade PVC pipes. These pipes meet the most stringent safety standards, ensuring that food products remain uncontaminated throughout the filling process. For general - purpose applications, we deploy PUC pipes. Both materials offer a suite of benefits including safety, non - toxicity, corrosion resistance, and heat resistance.
2. Customized Material Options:Understanding that different customers have diverse requirements, we offer the flexibility to choose from various materials. Whether you require a specific type of pipe for a particular production process or need to adhere to industry - specific regulations, we can accommodate your needs.
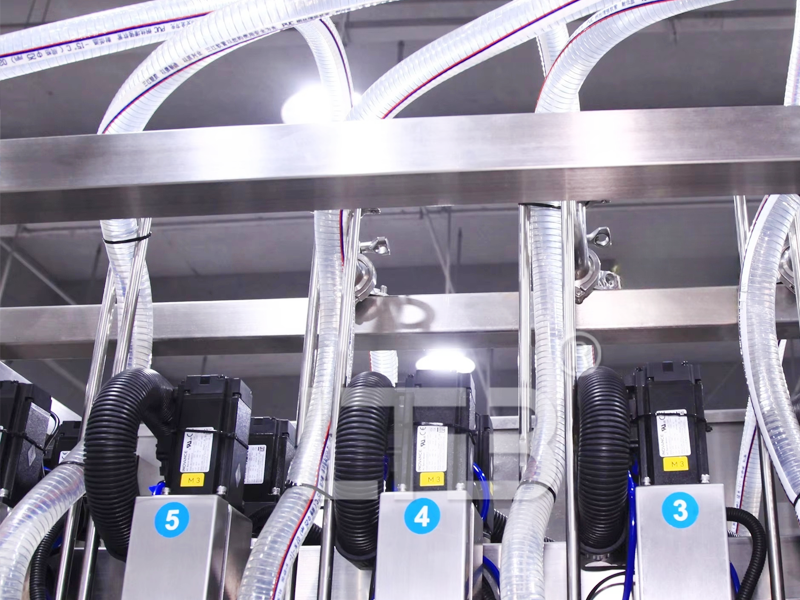
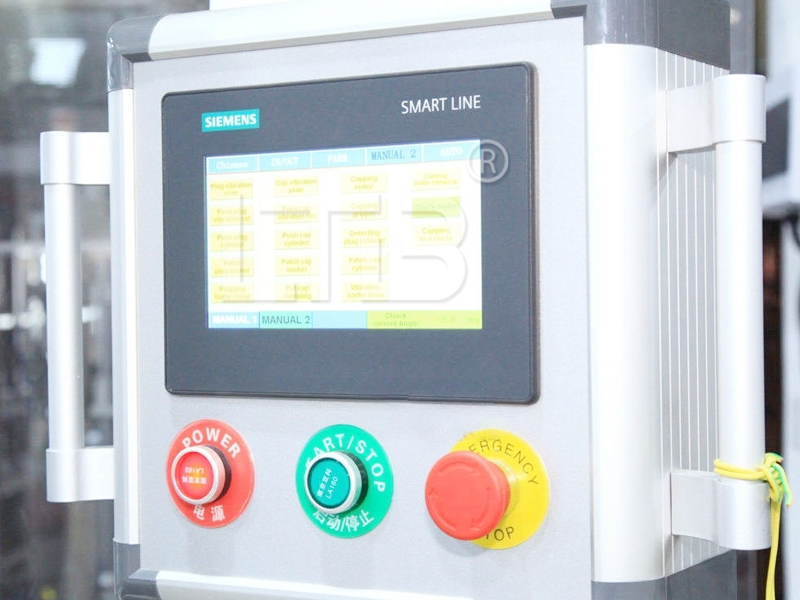
Smart Touch Screen
1. Superior Hardware Integration:Our filling machinery incorporates an imported Siemens touch screen. Recognized globally for its cutting - edge technology and unwavering reliability, this touch screen serves as the nerve center for seamless machine operation.
2. Outstanding Responsiveness and Precision:Characterized by its highly responsive interface, the touch screen ensures immediate interaction. This reduces the probability of input errors, contributing to smooth and efficient operation.
3. Intuitive Parameter Management:All machine - related parameters can be easily adjusted via the touch screen. The system comes with a built - in memory function, allowing it to store and recall customized parameter settings. This not only simplifies the operation process but also maximizes production flexibility, meeting diverse production demands.